关于精益生产管理的六个误区——你的企业是否踩坑了?
|
fangfang
2025年4月19日 15:20
本文热度 1650
|
精益生产(Lean Production)源自丰田生产方式(TPS),旨在通过消除浪费、优化流程来提升效率、降低成本。然而,许多企业在推行精益管理时,由于理解偏差或执行不当,不仅未能实现预期效果,反而陷入更深的运营困境。 精益生产管理中的六大常见误区,帮助企业避开陷阱,真正发挥精益管理的价值。 错误认知:一些企业认为“精益”就是裁员、减少开支,甚至盲目压缩员工数量。
过度裁员可能导致员工士气低落、技能断层,反而影响长期效率。 错误认知:许多人认为精益管理仅适用于工厂车间,与服务业无关。
精益的核心理念(如减少浪费、提升客户价值)适用于任何行业。 医院、物流、餐饮等行业均可通过精益优化流程(如缩短患者等待时间、减少配送冗余环节)。 服务业可借鉴5S管理、价值流分析(VSM)等工具; 错误认知:部分企业直接复制丰田模式,忽视自身行业特点。 丰田生产方式(TPS)是在特定历史背景下形成的,不同企业行业、规模、文化差异巨大。 学习精益原则(如JIT、持续改进),但需结合企业实际调整; 错误认知:一些管理者将精益视为“一次性运动”,认为完成几个改善项目就大功告成。 精益的本质是持续改进(Kaizen),需要长期坚持。 错误认知:部分企业过度追求效率提升,忽视员工参与度和满意度。 精益成功的关键在于全员参与,如果员工被动执行,改善难以持续。 错误认知:许多企业将精益简单等同于“5S”(整理、整顿、清扫、清洁、素养),认为做好现场卫生就万事大吉。
如果只做表面清洁,不解决流程浪费、库存积压等深层问题,效果有限。 在5S基础上,结合价值流分析(VSM)、看板管理(Kanban)等工具; 从“现场管理”升级到“系统优化”,实现真正的精益化。 精益生产不是一场“运动”,而是一种持续改进的管理哲学。企业若想成功推行精益,必须: 只有跳出误区,才能让精益管理真正助力企业降本增效、提升竞争力,在激烈的市场中立于不败之地! 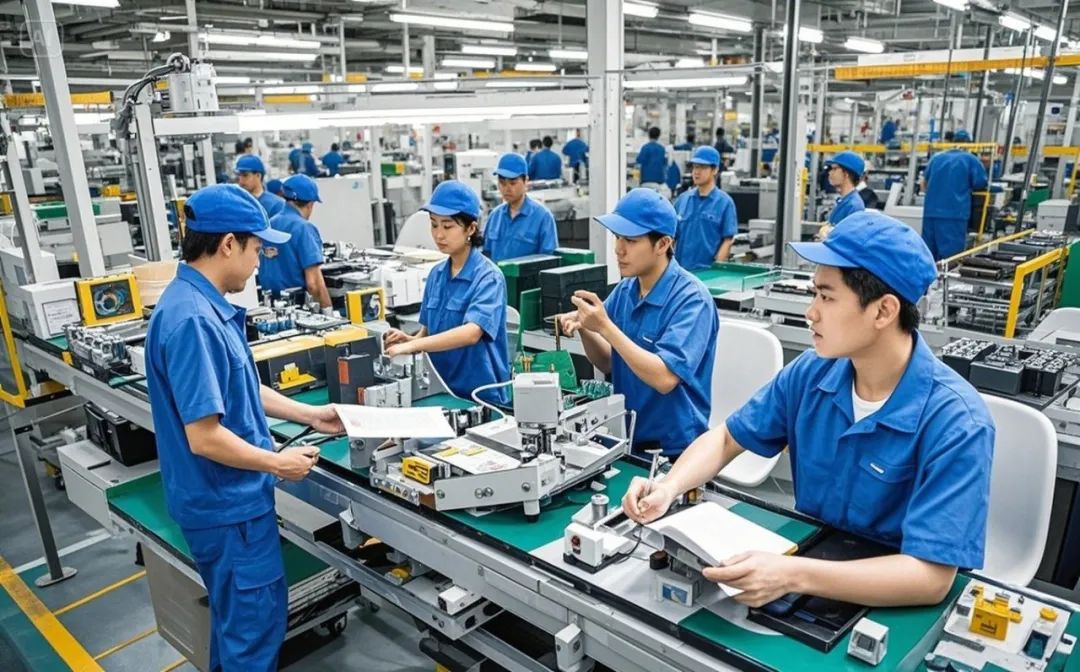
该文章在 2025/4/19 15:20:03 编辑过